SOLUTIONS
Application
What do End Mills coatings do
What do End Mills coatings do?
What is End Mills coating?
To put it simply, the coating is like the clothes of an end mill.On different occasions, it needs to be worn the right clothes. For example, people need to wear a spacesuit when they are in outer space, and a swimsuit when they swim. Therefore, depending on your processing conditions, it will affect what coating you need to choose.

The purposes of coating are:
✔️ Increase the hardness.
✔️ Increase lubricity.
✔️ Provide better chip evacuation.
✔️ Provide a thermal barrier.
✔️ Improve the surface finish.
✔️ Reduce abrasive wear.
✔️ Prolong the tool's life.
End Mills coating types(PVD & CVD)
Basically, there are 2 kinds of thin film deposition, Physical Vapor Deposition (PVD), and Chemical Vapor Deposition (CVD). Speed Tiger provides both of them, including over 10 types of PVD coatings.Let's take a look at their characteristics with a summary table:
Item | Coating Type | ALTIBN | TiSiN | ZrN-A | ZrN-S | nACo | TiSiN+ | P-nACo | nACro | SH (AlTiSiN) | SS (AlTiCrN) | RS (CrSiN) | TB |
Characteristic | Hardness (HV) | ~3400 | ~3600 | ~3400 | ~3600 | 45 (Gpa) | ~3600 | 47 (Gpa) | 42 (Gpa) | 3600 | 3300 | ~2800 | >6000 |
Thickness (IJm) | 2~4 | 2~4 | 2~4 | 2~4 | 2~4 | 2~4 | 2~4 | 2~4 | 2~4 | 2~4 | 2~4 | <1 | |
Oxidation Temp.(°C) | 900 | 1100 | 900 | 1100 | 1200 | 1100 | 1200 | 1100 | 1200 | 900 | 1000 | 500 | |
Friction Coefficient | 0.4 | 0.5 | 0.3 | 0.3 | 0.35 | 0.4 | 0.35 | 0.35 | 0.34 | 0.3 | 0.3 | <0.1 | |
Color | Black | Copper | Golden | Golden | Blue | Copper | Blue | Gray | Golden | Silver | Silver | Black | |
Application |
Carbon Steel | ⊚ | ⊚ | ⊚ | ⊚ | ⊚ | ⊚ | ⊚ | ⊚ | ⊚ | 〇 | ⊚ | X |
High Speed Steel | 〇 | 〇 | ⊚ | ⊚ | ⊚ | 〇 | 〇 | ⊚ | ⊚ | ⊚ | ⊚ | X | |
Stainless Steel | 〇 | 〇 | ⊚ | ⊚ | ⊚ | 〇 | 〇 | ⊚ | 〇 | ⊚ | ⊚ | X | |
Alloy | ⊚ | ⊚ | ⊚ | ⊚ | ⊚ | ⊚ | ⊚ | ⊚ | ⊚ | 〇 | 〇 | X | |
Copper / Aluminum | X | X | X | X | X | X | X | 〇 | X | X | 〇 | ⊚ | |
Inconel | ⊚ | ⊚ | ⊚ | ⊚ | ⊚ | ⊚ | ⊚ | 〇 | ⊚ | 〇 | 〇 | X | |
Titanium | 〇 | 〇 | 〇 | 〇 | 〇 | 〇 | 〇 | 〇 | 〇 | ⊚ | |||
Plastic / Composites/ Wood / Paper |
X | X | X | X | X | X | X | X | X | X | X | ⊚ | |
Cutting Way | Dry Cutting | ⊚ | ⊚ | ⊚ | ⊚ | 〇 | ⊚ | 〇 | 〇 | 〇 | 〇 | ⊚ | 〇 |
Wet Cutting | 〇 | 〇 | 〇 | 〇 | 〇 | 〇 | 〇 | 〇 | 〇 | ⊚ | ⊚ | ⊚ | |
Oil Spray | 〇 | 〇 | 〇 | 〇 | ⊚ | ⊚ | ⊚ | ⊚ | 〇 | ⊚ | 〇 |
Common Endmills coatings with Speed Tiger
The 5 coatings most commonly used with Speed Tiger's End Mills:
1.ALTIBN Coating |
A. Coating Structural Analysis – SEM
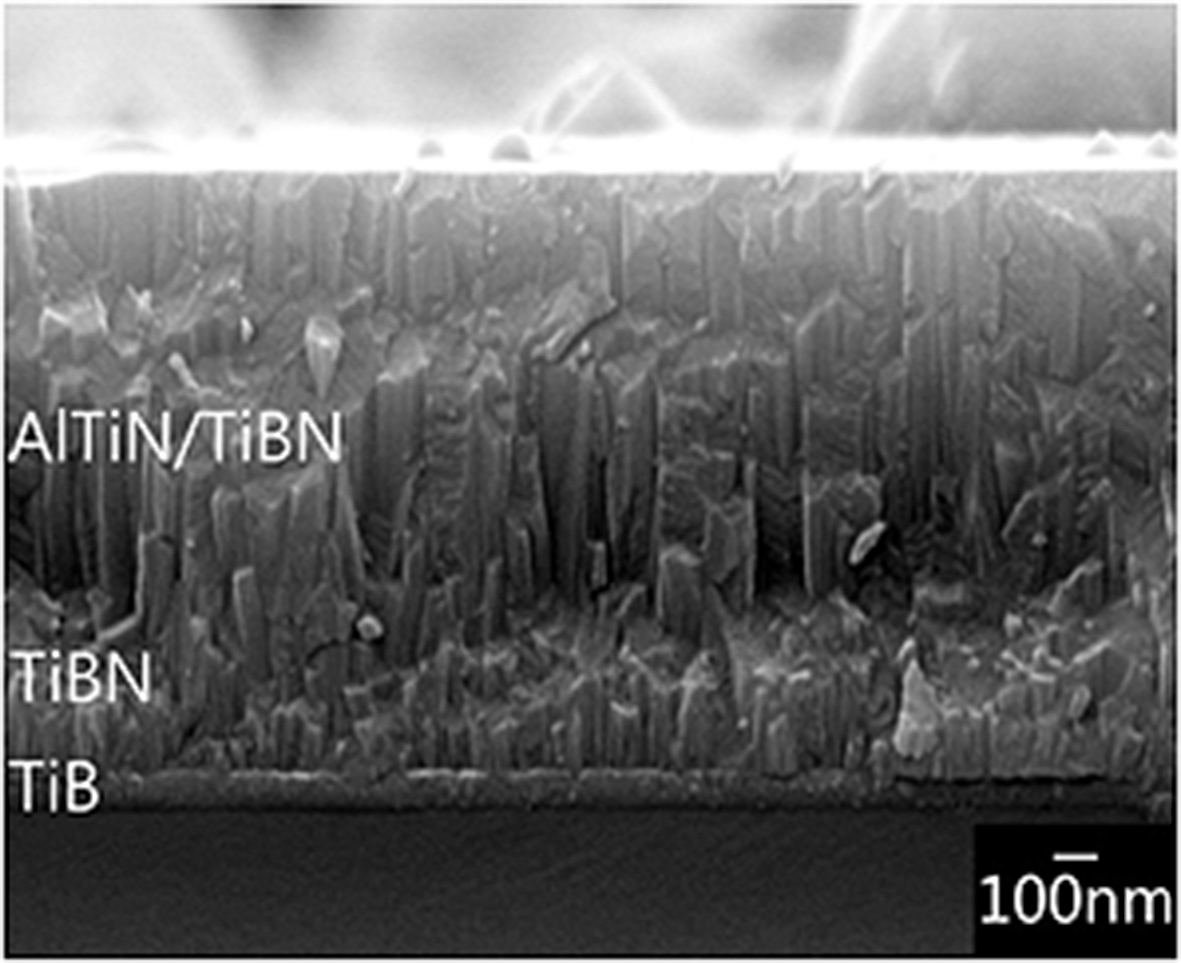
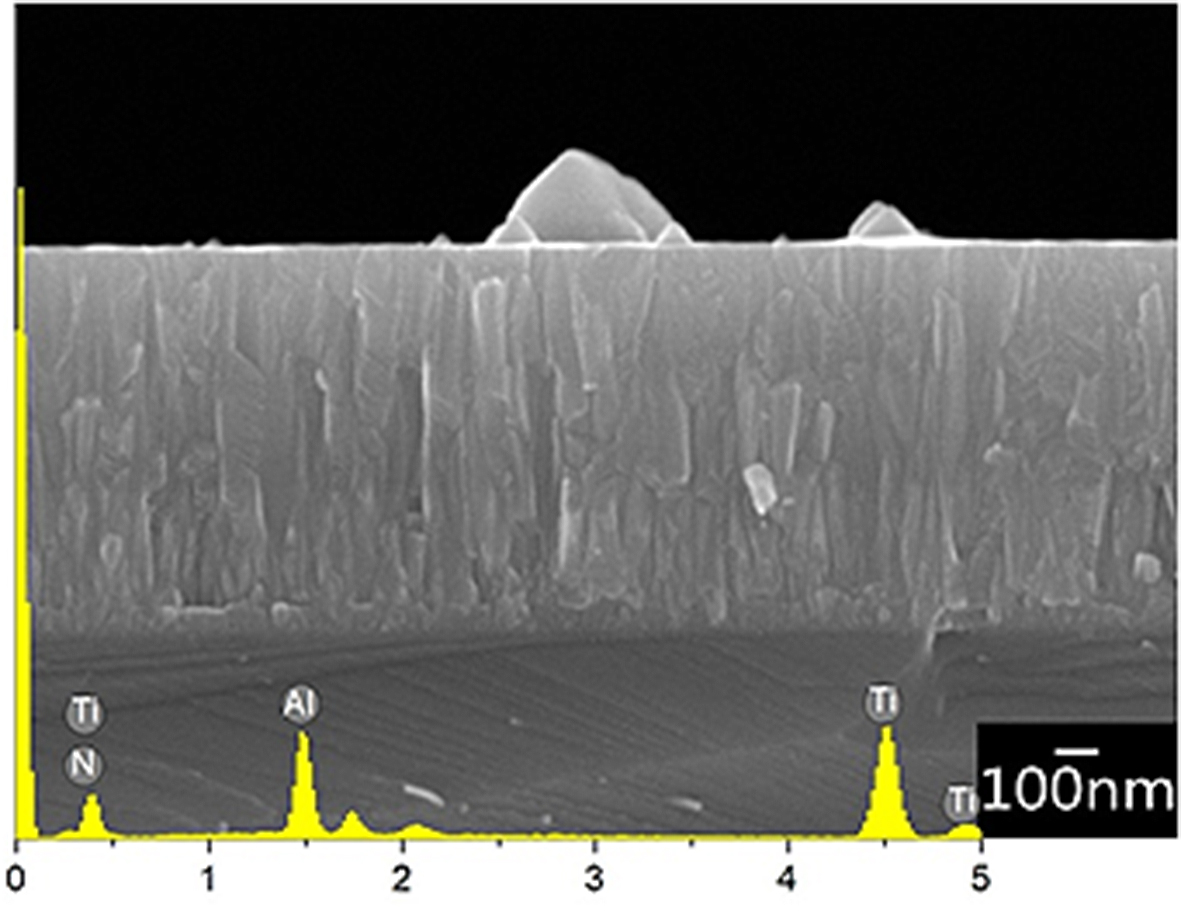
B. Normal Temperature – Mechanical Analysis
Hardness(HV) | Impact of Diameter | Lc2-Lc1 | Wear Rate | Roughness | |
AlTiN | 3672 | 305(µm) | 8.28N | 6.49x10-6 | 0.233 |
AlTiBN | 4088 | 280.9(µm) | 17.6N | 5.11x10-6 | 0.166 |
C. The Oxidation Wear of 700°C
In normal temperature mechanical analysis, the performance of AlTiBN is superior to AlTiN in hardness, wear rate, and coating roughness.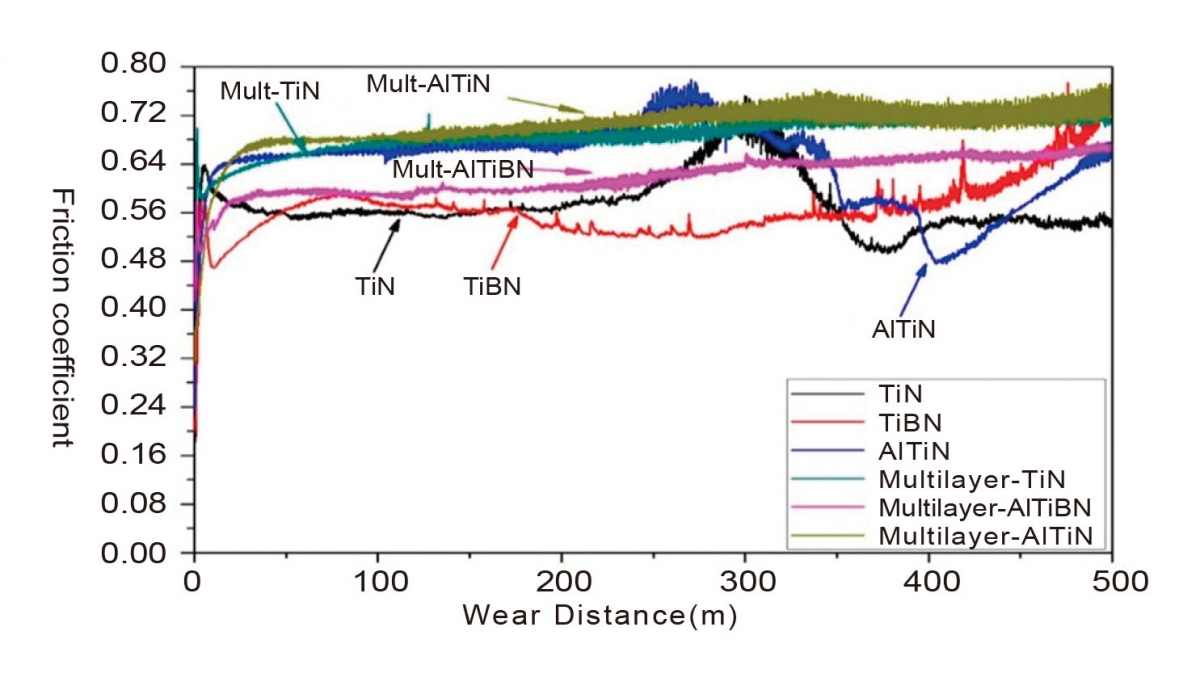
The wear rate of AlTiBN at high temperatures is also superior to the above coatings.
Friction Coefficient | Wear Distance | Wear rate | |
TiN | 0.5662 | 316.3 | 6.4x10-6 |
TiBN | 0.5664 | 281.2 | 5.69x10-6 |
AlTiN | 0.6402 | 281.4 | 4.97x10-6 |
Mult-TiN | 0.686 | 277.4 | 4.82x10-6 |
AlTiBN | 0.618 | 281.8 | 4.66x10-6 |
Mult-AlTiN | 0.7014 | 290.1 | 5.5x10-6 |
D. Tool Life Comparison
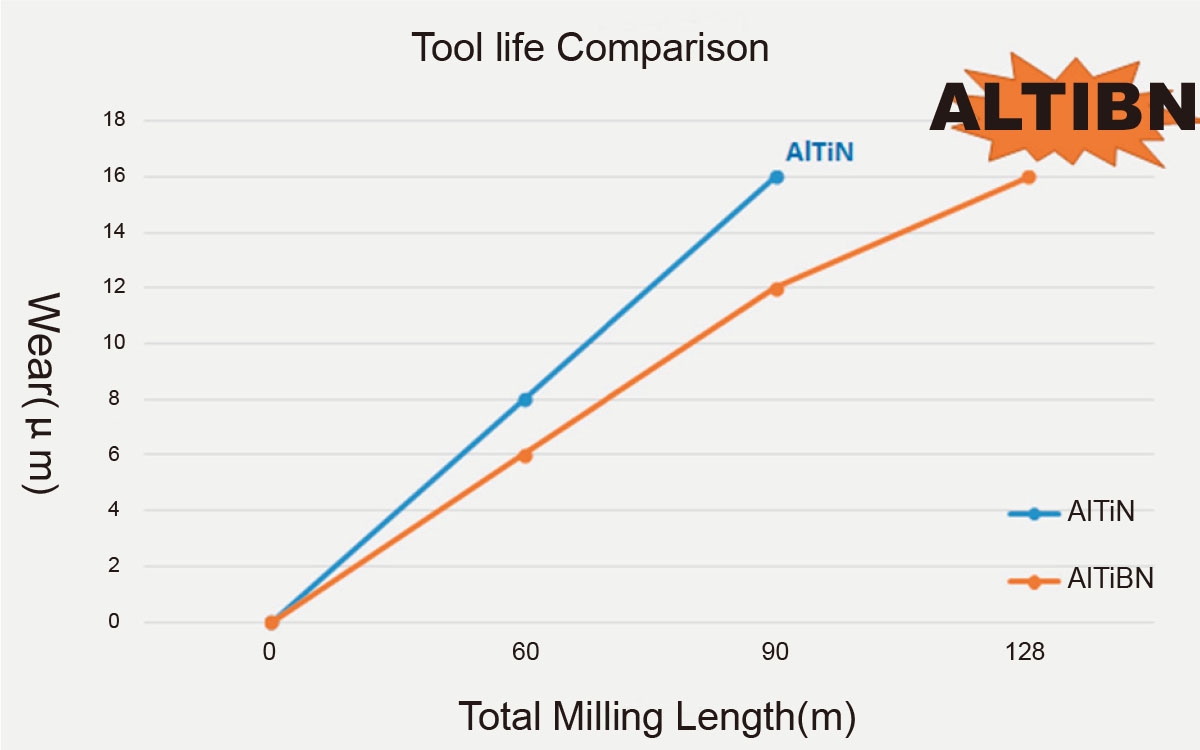
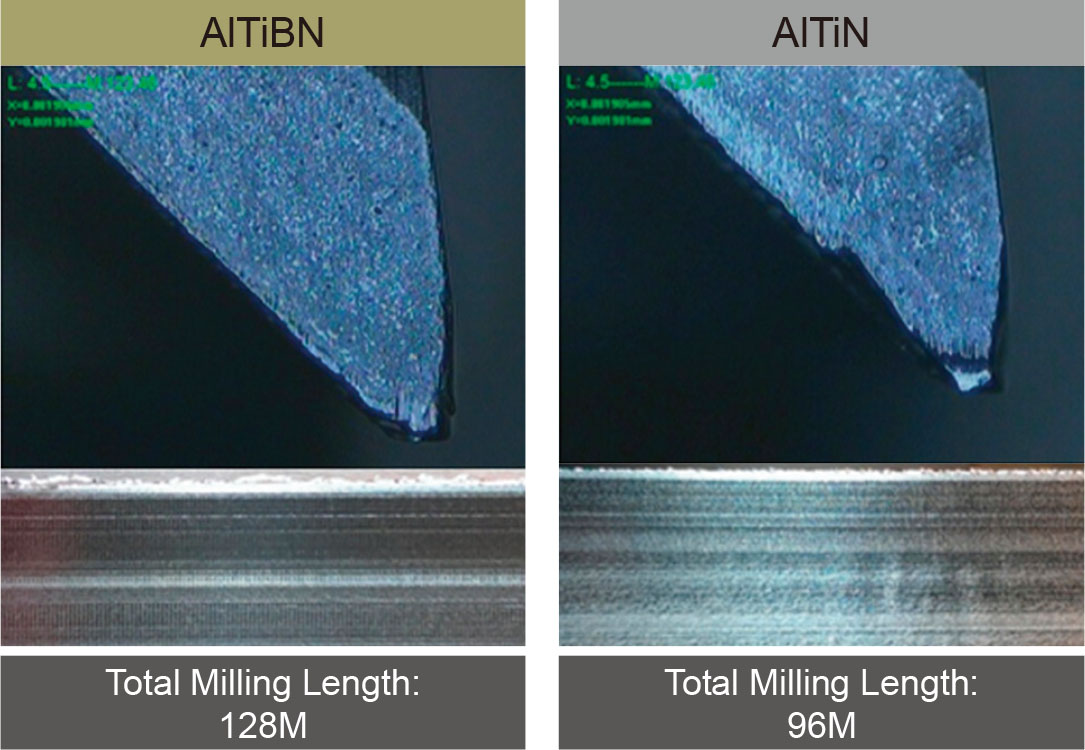
2. TiSiN Coating |
New Nano-composite coating material achieves extraordinary heat resistance and hardness. This is attained due to the new composite layer, consisting of nano-crystal material
(Oxidizing temperature: 1100°C, Layer hardness: HV 3600).
Achieves extraordinary performance in high-speed cutting, and high efficient machining of hardened steel, machining efficiency is more than twice as effective as other manufacturers'
solid carbide end mills. Ensuring long life and reliability in hardened steel applications HRC45~55 material examples: 1.2080, 1.2344, and 1.2379, ASP Power Steels, High Speed Steels.
The coating generates less heat during cutting; therefore it is well suited to dry machining conditions.
Newly developed TiSiN Coating has excellent oxidation-resistant properties, this achieves High speed cutting of hard steels = High-Efficiency Improvement in tool life = Lower tooling costs.
The newly designed flute geometry increases rigidity, with the improved high radius accuracy producing higher tolerance, and smoother surface finish.
Direct Milling of hardened steel is now possible = Faster production times.
(Oxidizing temperature: 1100°C, Layer hardness: HV 3600).
Achieves extraordinary performance in high-speed cutting, and high efficient machining of hardened steel, machining efficiency is more than twice as effective as other manufacturers'
solid carbide end mills. Ensuring long life and reliability in hardened steel applications HRC45~55 material examples: 1.2080, 1.2344, and 1.2379, ASP Power Steels, High Speed Steels.
The coating generates less heat during cutting; therefore it is well suited to dry machining conditions.
Newly developed TiSiN Coating has excellent oxidation-resistant properties, this achieves High speed cutting of hard steels = High-Efficiency Improvement in tool life = Lower tooling costs.
The newly designed flute geometry increases rigidity, with the improved high radius accuracy producing higher tolerance, and smoother surface finish.
Direct Milling of hardened steel is now possible = Faster production times.
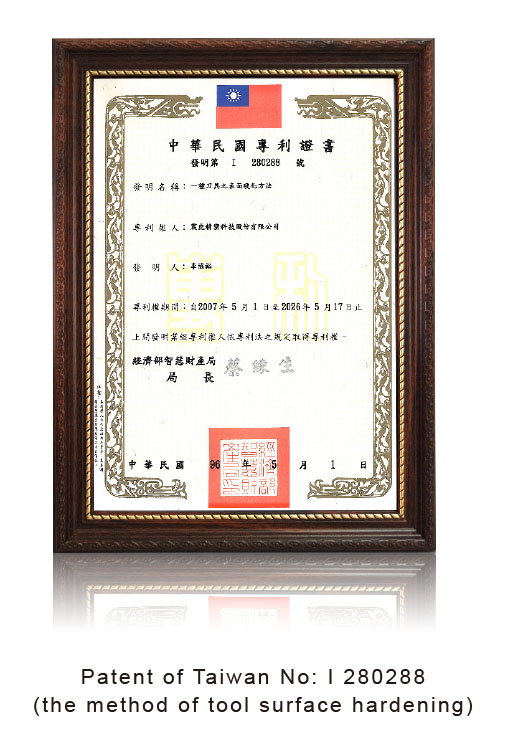
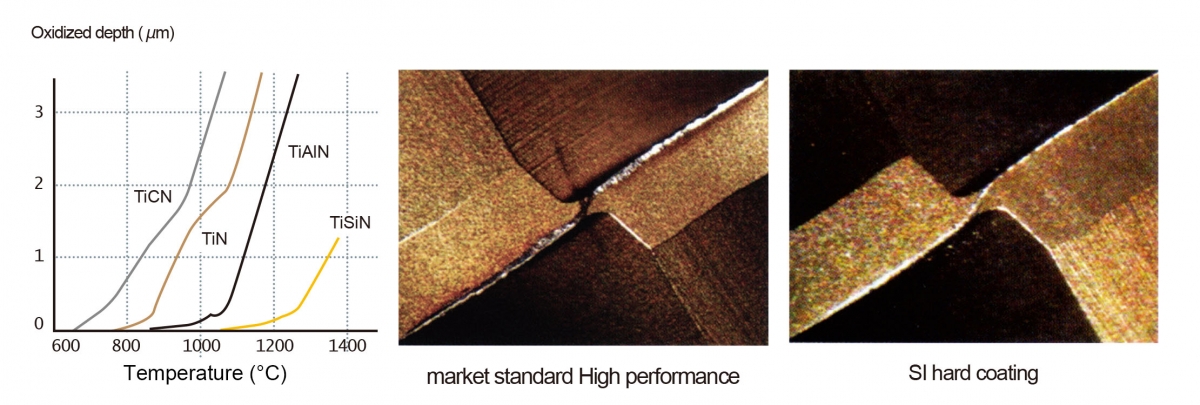
3. ZrN-A Coating |
A. Anti-resistance:
Suitable for High-Speed machining with both dry and wet cutting ways.B. Good for stainless steel cutting.
- Hardness 2800~3000 HV
- Coefficient of friction: 0.3
- Oxidation Temp.: 800~900°C
- High-performance coating (Light golden)
C. Test Result
SUS316 Slotting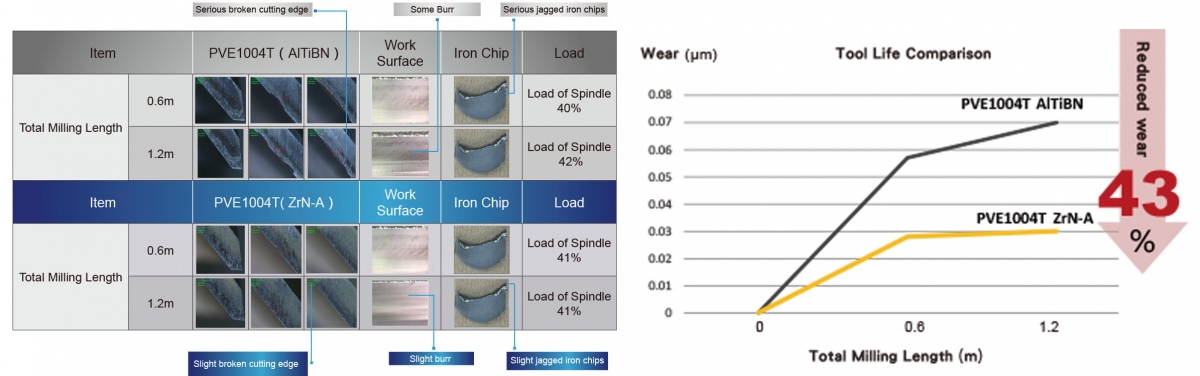
4. nACo Coating |
✔️Perfect coating structure.
✔️High hardness.
✔️High adhesion.
✔️Adding Si into nACo structure makes the atom structure more complete with high hard-wearing and tools with much longer life
A. Heat Resistance Comparison
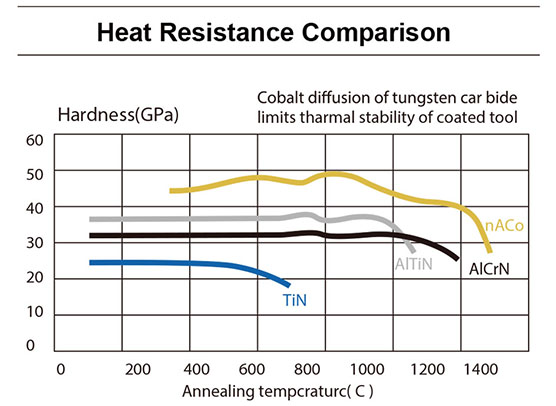
B. Tool Life Comparison
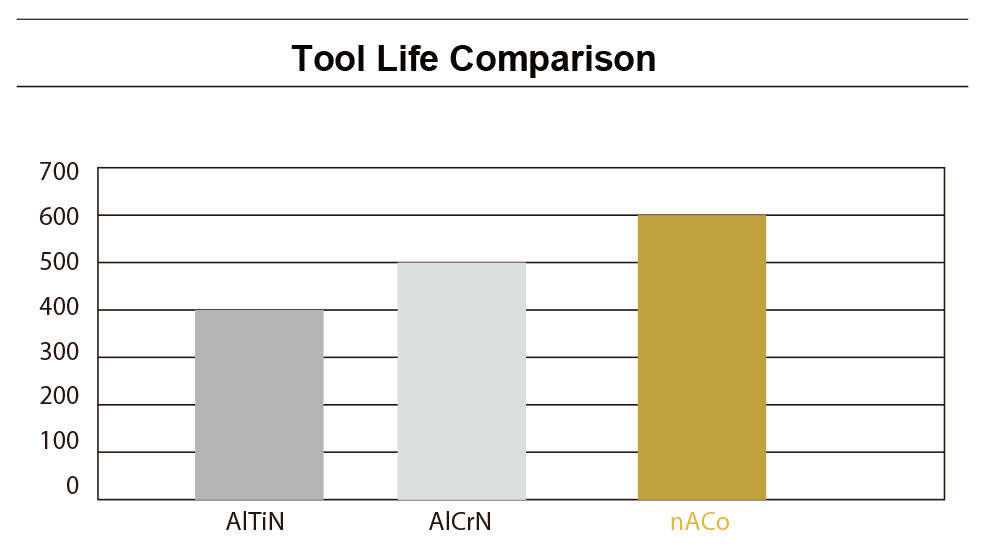
C. AlTiN V.S nACo
Coating | Thickness(µm) | Hardness (GPa) | Oxidation Temp.(°C) | Friction Coefficient |
AlTiN | 2~4 | 35 | 800 | 0.6 |
nACo | 2~4 | 45 | 1200 | 0.35 |
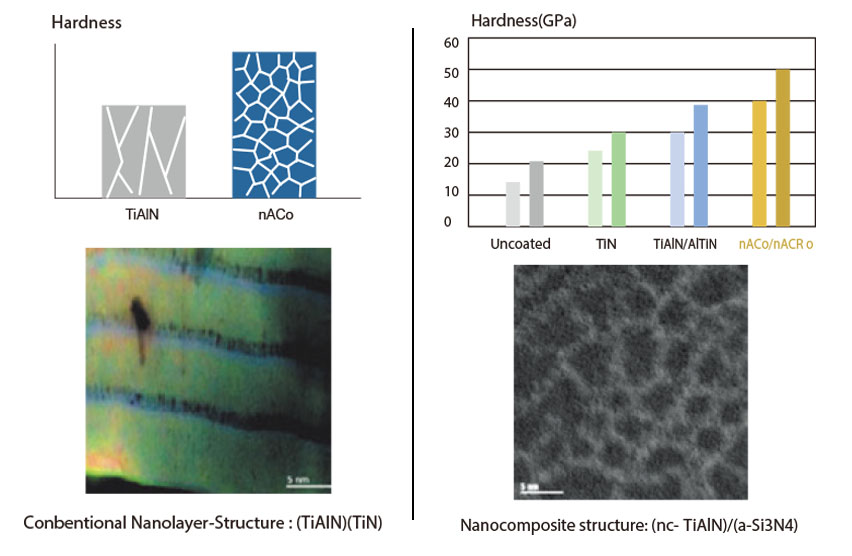
D. Hardness Increase though Nanocomposites
5. nACro Coating |
✔️Contain Si membrane, oxidation start temperature: 1,100°C
✔️Nano grade coating, better surface finish.
✔️Extremely high Nano hardness, extremely high adhesion.
✔️Better protection for tools, reduction of production cost, economical environmentally manufacturing.
By deposition very different kinds of materials, the components (like Ti, Cr, Al in the first group, and Si in the other) are not mixed completely, and 2 phases are created. The nanocrystallineTiAlN- or AlCrN-grains become embedded in theamorphous SiN-matrix and the nano-composite structure develops.
Silicon increases the toughness and decreases the internal residual stress of the coating. The increasing of the hardness is generated by the structure only, the SiN matrix enwraps the hard grains and avoids growing of their size.
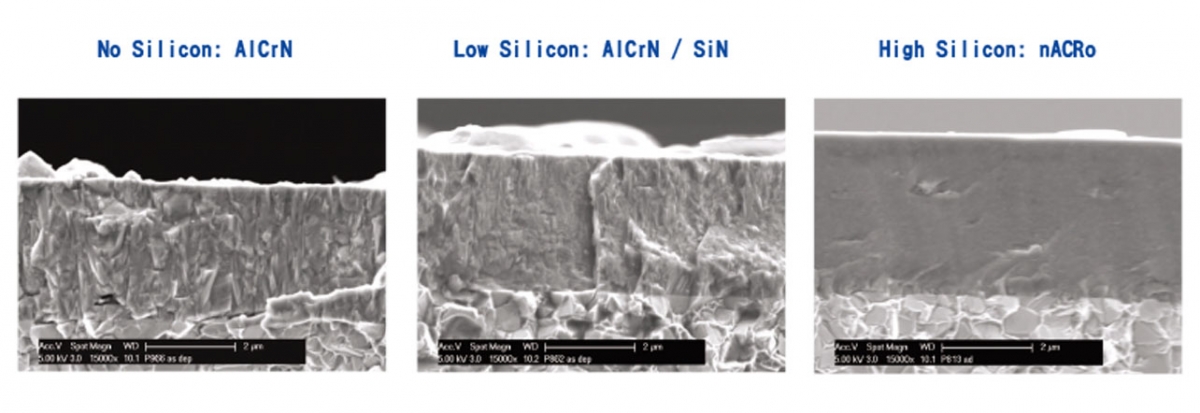
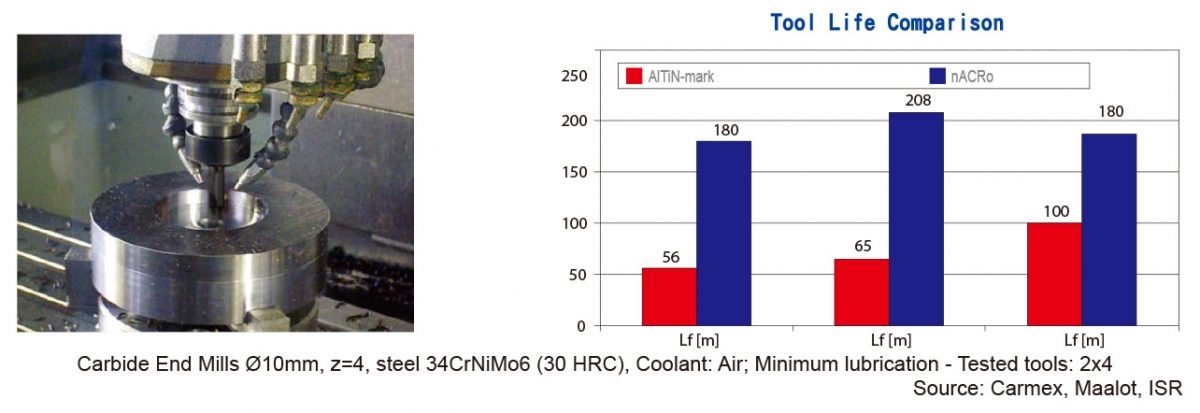
6. TB Coating = Tetrabond Diamond Coating (DLC) |
✔️Super high lubrication & Super low friction coefficient
✔️New PVD Nano Technology
✔️The tool is a long life to be surprised because TB hardness to near the nature diamond coating
✔️Swiss & Speed Tiger Technological Cooperation.
Application: Excellent cutting is reached in machining non-ferrous materials, especially in aluminum with over six multiple in machining efficiency. Long tool life and precision machining in PCB boards, Brass, Titanium, Ceramics, Fiberglass, etc.
DLC coatings are generally deposited by five methods, each having different properties, especially on Hardness and Oxidation:
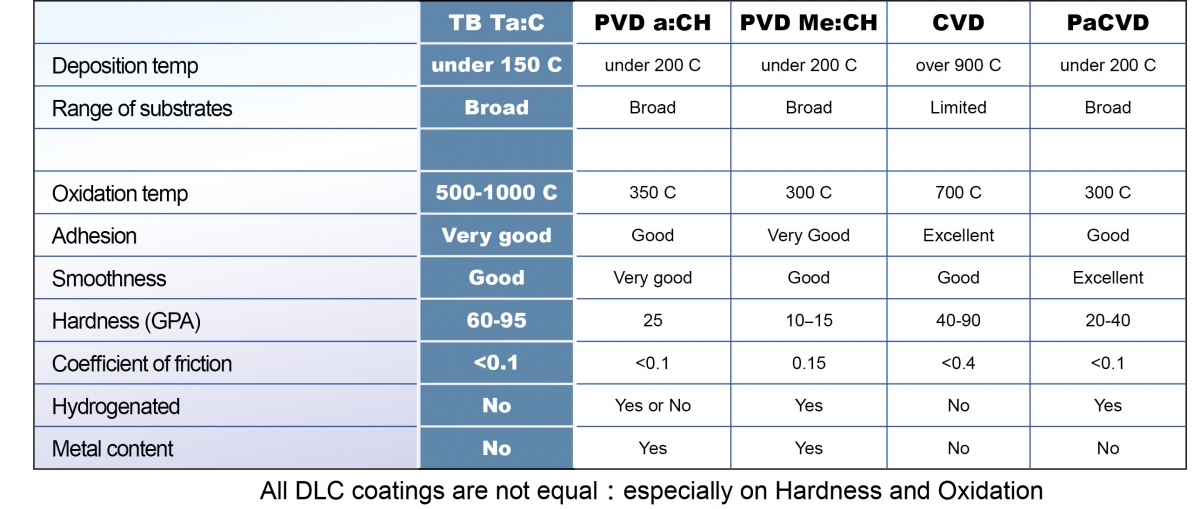
Application: Excellent cutting is reached in machining non-ferrous materials, especially in aluminum with over six multiple in machining efficiency. Long tool life and precision machining in PCB boards, Brass, Titanium, Ceramics, Fiberglass, etc.
Related Articles: The Guide of End Mill for Aluminum Machining.
Related Products Info: |
Custom End Mill, Build a Custom Tools for your Job!
End Mill Size Standards Chart & Introduction
Speed Tiger is the leading Carbide End mills manufacturer in Taiwan, we provide a large range of CNC End mills, see more end mills products by clicking this photo!
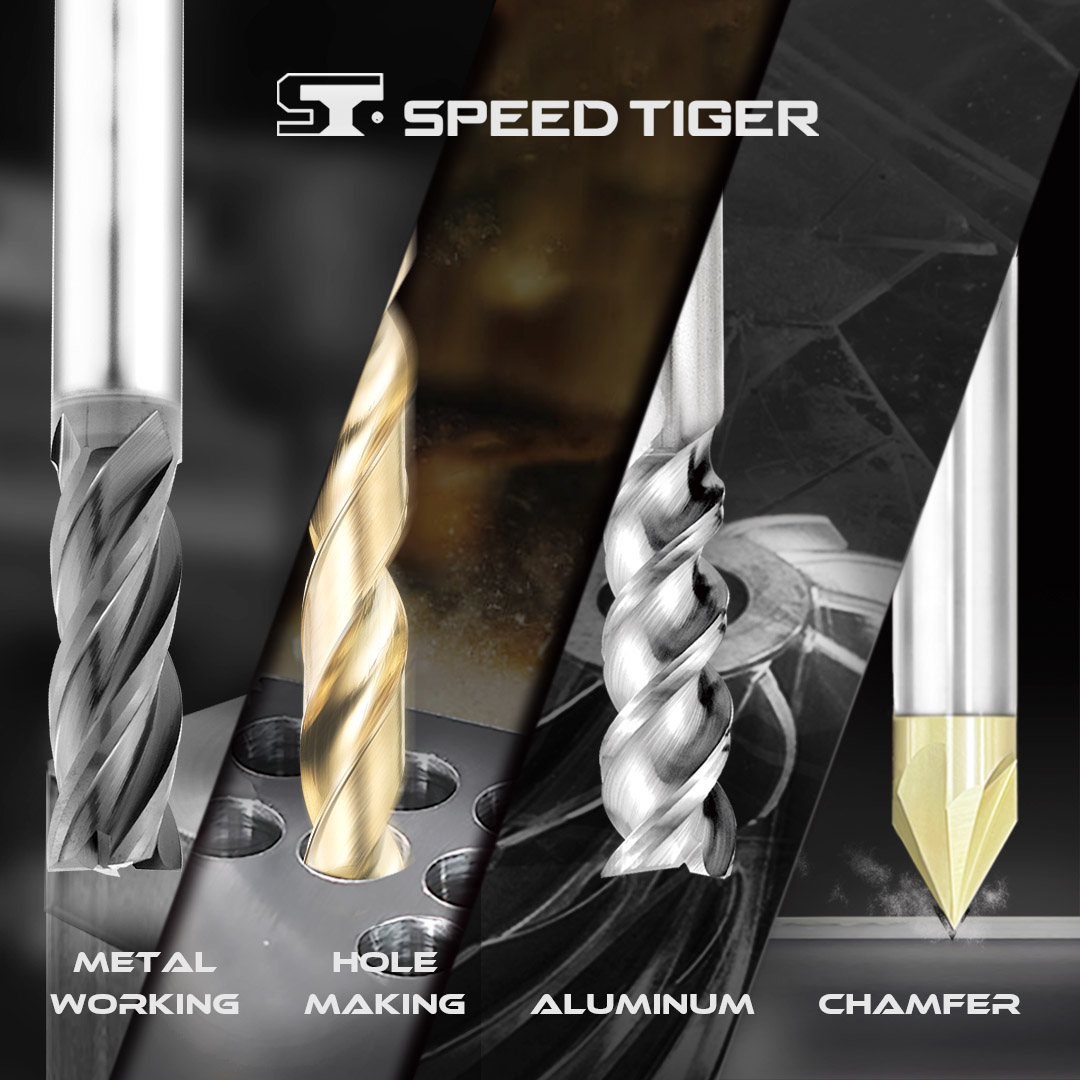
About Speed Tiger |
Speed Tiger is a professional manufacturer of Carbide Cutting Tools and offers OEM Services, having rich experience in producing carbide cutting tools and processing consultants for more than 24 years.
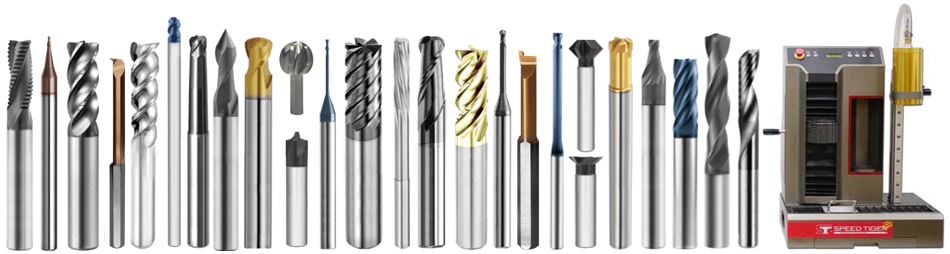
Established in 1998, Speed Tiger specialized in the production of precision carbide end mills, drills, turning tools, thread mills, and other tungsten carbide steel customized cutting tools. Speed Tiger crafts cutting tools at extreme nanometer precision +-2㎛ to the exact, enabling to achieve professional cutting quality.
Visit our shop to find out more, or check out our solution to continue learning.
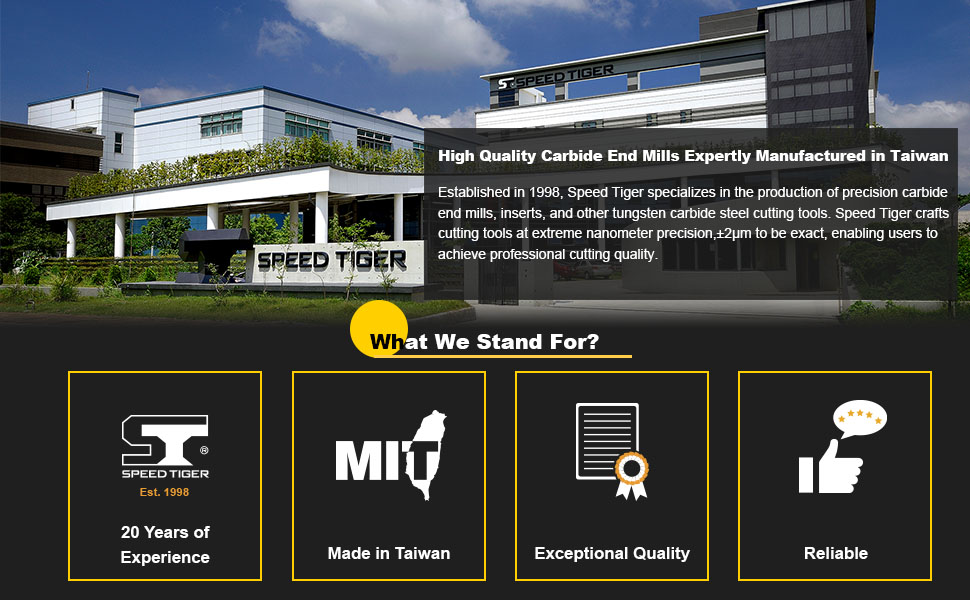
OTHER SOLUTIONS
-
When Should I Use Flat Drills (Flat Bottom Tools) ? Posted 2021-04-09