SOLUTIONS
Knowledge
Master Guide of Roughing & Finishing Cut in Machining (Differences & Usage)
Master Guide of Roughing & Finishing Cut in Machining (Differences & Usage)
Machining or cutting consists of a number of stages, taking a raw piece of material from its initial state to the desired object that it is intended to be. Multiple techniques are used to obtain the final result to ensure it is the right shape and size and have the right finishing. The processes used consist of categories such as conventional machining, abrasive cutting, micro-precision machining, and non-traditional machining. Two of the initial stages in machining are the rough cut and finishing cut, which shape the material and improve the finish of the surface. Both of these are important processes but it's important to understand the differences between them and when each one should be used.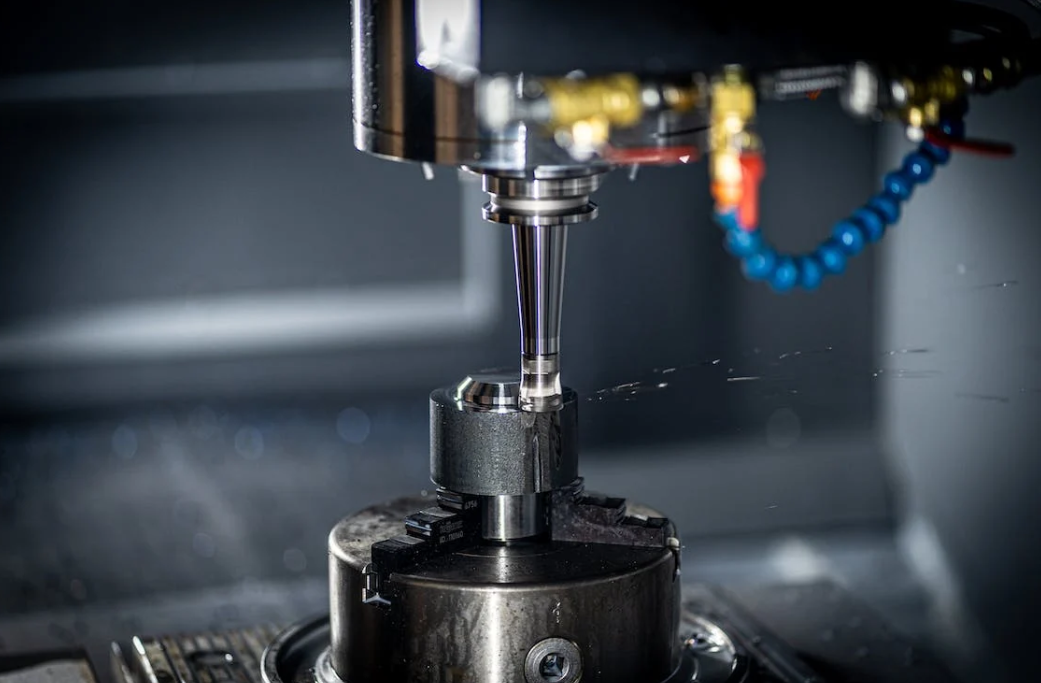
So, we have created this complete guide that tells you everything you need to know about Roughing & Finishing Cut in Machining (Differences & Usage).
- Why Is Material Cutting Needed in Machining?
- Why Need to Distinguish Between Roughing & Finishing in Machining?
- What is Roughing Cut in Machining?
- What is Finishing Cut in Machining?
- Differences Between Roughing (End Mill) and Finishing (End Mill) in Machining
- Roughing End Mill vs. Finishing End Mill
- Tips for Choosing the Right Roughing and Finishing End Mill Cutter
Why Is Material Cutting Needed in Machining?
Machining or metal cutting uses a variety of processes to gradually remove material from a blank and eventually produce the finished product. Material can be removed layer by layer and in different amounts, as well as using different levels of precision. Some processes are used to remove bulk amounts of material, while others are designed to finish the material more smoothly or complete smaller levels of detail.Multiple cuts or passes are typically required to achieve both the removal of material and the desired high-quality finish. Conventional machining processes such as turning, threading, drilling, and milling are used to remove larger amounts of material and can generally provide a decent finish too. However, this requires multiple stages to achieve both.
- The first step is the rough pass, which is used for stock removal.
- The second step is the finishing cut, which can improve the surface finish, as well as the tolerance level and dimensional accuracy.
Why Need to Distinguish Between Roughing & Finishing in Machining?
Roughing and finishing in machining are two key stages to complete the machining timeline. They are used for two different purposes, first removing material and then finishing the surface area.By splitting roughing and finishing into two distinct stages, it's possible to make the most of each type of machinery. Roughing equipment has more power and efficiency while finishing equipment is built for accuracy and reducing error.
What is Roughing Cut in Machining?
Roughing is used to remove bulk material quickly and to start creating a rough shape for the finished product. The aim of the rough cut is not to provide accuracy or finish the surface smoothly but to quickly remove material. It usually leaves a rough finish but the benefit is that it is carried out efficiently to get the job done quickly.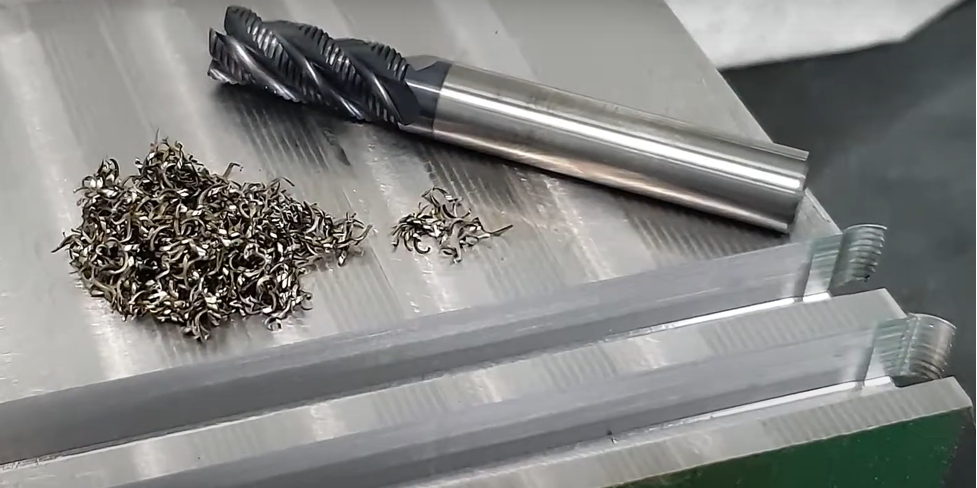
What is Finishing Cut in Machining?
After roughing, finishing can be used to create a better finish for the surface of the material. The main shape of the part has already been fabricated, and finishing is then used to change the surface texture and finish. It can help to remove defaults and improve the appearance, as well as have the practical benefits of improving performance or imparting specific mechanical properties. Finishing can include processes such as precision machining, grinding, polishing, electroplating, and more.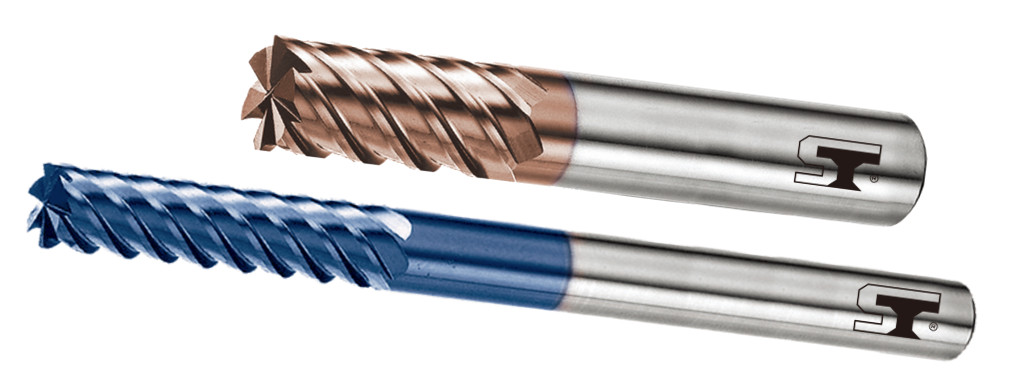
Differences Between Roughing (End Mill) and Finishing (End Mill) in Machining
The differences between roughing and finishing end mills are important to note when finding the right option for each application. There are several key differences to note so that you can choose the best type for any machining project.
Material Removal Rate
The rate of material removal is important to note in both roughing and finishing end mills. Roughing end mills have a high rate of material removal, while finishing end mills have a lower rate, in comparison. This means that each is best for different applications, rather than giving one a complete advantage over the other.Feed Rate
The feed rate is another key factor when choosing between roughing and finishing end mills. Roughing end mills have a higher feed rate, which means that you can work quickly with them. The lower feed rate and cutting depths of finishing end mills help to make them the better choice for their purpose.Surface Finish
The beneficial qualities of roughing end mills also mean that the surface finish they provide is not that smooth. Due to its high feed rate and depth of cut, a roughing end mill will result in more visible feed marks. This leaves a rougher surface, which isn't necessarily suitable for the desired end product. On the other hand, finishing end mills have a lower feed rate and make shallow cuts for an improved surface finish.Accuracy and Tolerance
Roughing end mills aren't capable of providing accuracy and close tolerances because they are not as precise as finishing end mills. Finishing end mills can deliver high dimensional accuracy and requirements for close tolerances, which makes them a better choice for this purpose.Cutter Type
The sharpness of cutters is another factor that affects the results that can be achieved by different types of end mills. Roughing end mills don't need to have cutters with very sharp edges and can take a high chip load because the quality of the surface finish isn't the top priority for a rough cut. However, finishing end mills need to have sharper cutters with a low chip load so that they can achieve a smoother finish.Roughing End Mill vs. Finishing End Mill
End mill tools can be used for a variety of machining applications. They are useful for both roughing and finishing purposes, but different end mills need to be used to achieve each task.What Is a Roughing End Mill?
A roughing end mill is designed for carrying out the rough cut. They are also sometimes called hog mills and can remove large amounts of material. Roughing end mills have a design with teeth which helps to reduce vibration but also leaves a rougher finish.►Pros of Roughing End Mills
- Fast feeding can be realized to complete machining quickly and efficiently
- The material removal rate is high
- Any defects can be identified and either repaired or scrapped quickly
- The design reduces vibrations for quieter operation and an efficient cut
- A higher depth of cut can be achieved
- Can use cutters with less sharp edges that take a high chip load
►Cons of Roughing End Mills
- A rough finish is left, requiring a finishing pass to make improvements
- Less accuracy and tolerance are possible compared to finishing end mills
What Is a Finishing End Mill?
Finishing end mills are designed to carry out finishing, helping to provide an improved surface. Instead of the tooth design of a roughing end mill, a finishing end mill is smooth. Finishing end mills can remove large amounts of material while also leaving a smoother finish. This means that roughing and finishing can sometimes be completed in one step, instead of splitting the process in two.►Pros of Finishing End Mills
- Improved surface finish
- A low feed rate can make it a good choice for beginners
- Higher dimensional accuracy compared to roughing end mills
- Can provide close tolerance levels
- A low amount of material removed
►Cons of Finishing End Mills
- Lower feed rates and cutting depths aren't suitable for all applications
- Sharp cutters that take a low chip load are required
- Finishing can only be carried out after roughing has been completed
Tips for Choosing the Right Roughing and Finishing End Mill Cutter
Selecting the right roughing and finishing end mill for any task is important. If you make a poor choice, you can find that you don't get the results you require, which could waste a lot of time and money. Here are some of the things you should take into account if you're choosing a roughing or finishing end mill.Process Parameters
It's important to consider the parameters of the process when choosing a roughing or finishing end mill. Cutting velocity, feed rate and the depth of cut are all factors to take into account. The diameter of the cut is another thing to consider. It's important to both use your CNC software to set the right parameters and choose a suitable end mill to get the job done.Operating Materials
The material being worked on and the material of the end mill are both essential to consider. When you know the material that needs to be cut, you can choose the best end mill based on how the material behaves and its characteristics. Additionally, the material of the tool itself makes a difference. High-speed steel is often a good choice when working with a lower budget, although cobalt and carbide can both provide higher performance.Performance and Durability
A quality end mill should be capable of machining at high speeds and temperatures. Any coatings should be designed to resist oxidation, which will expand the lifespan of the tool. Edge preparation is also an important consideration. A rounded edge helps to prevent cracking and minimizes wear, while also ensuring an even abrasion.Coating
The coating of the end mill should be taken into account to ensure durability. There are different types of coating available, which can have advantages such as extending the lifespan or reducing the amount of lubrication required.Related Article: How to choose the right Coating for your End Mill?
Roughing and finishing cuts are both important in machining. It's crucial to determine which tools should be used for each process to achieve the best results.
■ More Information & Tips about CNC End Mill:
Related Article: The Beginners Guide of CNC End Mill
If you are new to CNC processing, you may think that there are so many end mills in the catalog, what’s the difference? And which end mill should I use on my CNC machine? You will learn the basic knowledge of CNC end mills about End Mill Shapes, End Mill Flutes, Detail of the end mill, and End Mill Coatings.
Related Article: End Mill Cutting & End Milling - Technical Guide
End mills are a key tool for cutting, with a range of different applications. As one of the most common types of cutting tools, end mills are also unique and specifically used for the end milling process. End mill cutting and end milling are crucial in manufacturing, and being familiar with these processes and tools is a must.
Related Article: Master Guide of CNC Milling: Process & Application
If you are new to CNC milling, you have probably heard of this term but be unsure what it means. In this article, you will find all the information you will need to understand what CNC milling is, how it works, its applications, advantages, and more. Read on to discover everything you need to know about CNC milling.
About Speed Tiger |
Speed Tiger is a professional manufacturer of Carbide Cutting Tools and offers OEM Services, having rich experience in producing carbide cutting tools and processing consultants for more than 24 years.
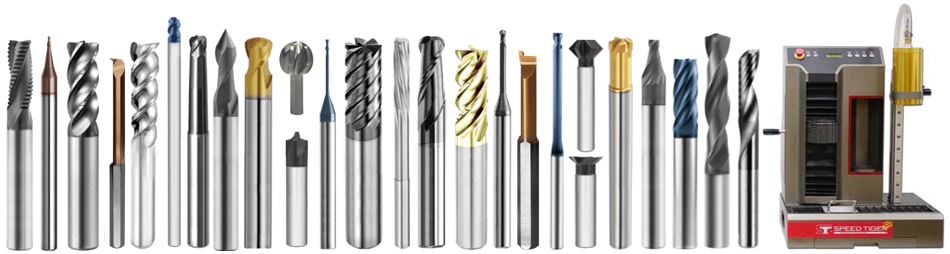
Established in 1998, Speed Tiger specialized in the production of precision carbide end mills, drills, turning tools, thread mills, and other tungsten carbide steel customized cutting tools. Speed Tiger crafts cutting tools at extreme nanometer precision +-2㎛ to the exact, enabling to achieve professional cutting quality.
Visit our shop to find out more, or check out our solution to continue learning.
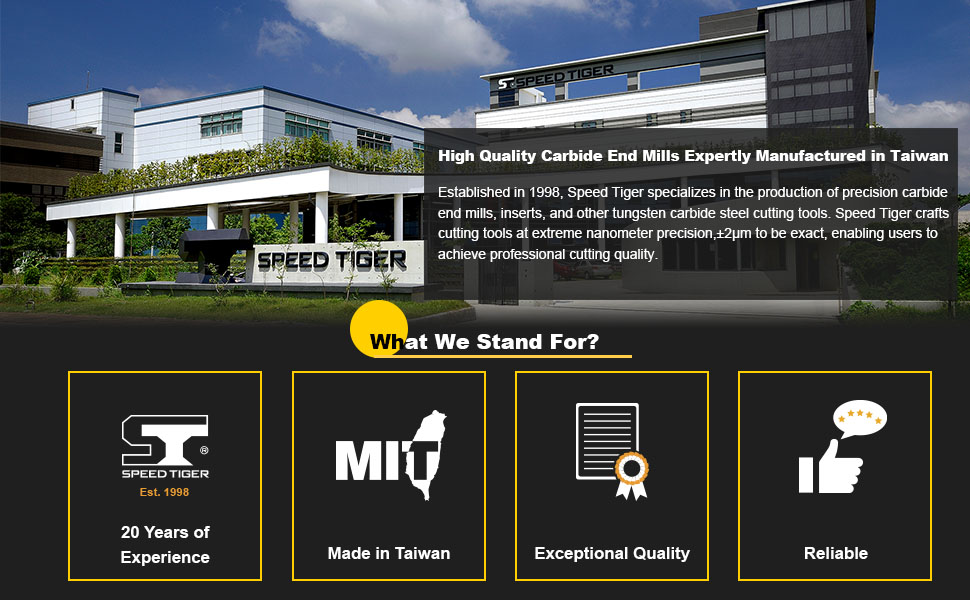
OTHER SOLUTIONS
-
Master Guide of CNC Milling: Process & Application Posted 2023-06-07
-
Guide to Selecting an End Mill for Aluminum Machining Posted 2022-06-30