SOLUTIONS
Knowledge
End Mill Cutting & End Milling - Technical Guide
End Mill Cutting & End Milling - Technical Guide
End mills are a key tool for cutting, with a range of different applications. As one of the most common types of cutting tools, end mills are also unique and specifically used for the end milling process. End mill cutting and end milling are crucial in manufacturing, and being familiar with these processes and tools is a must.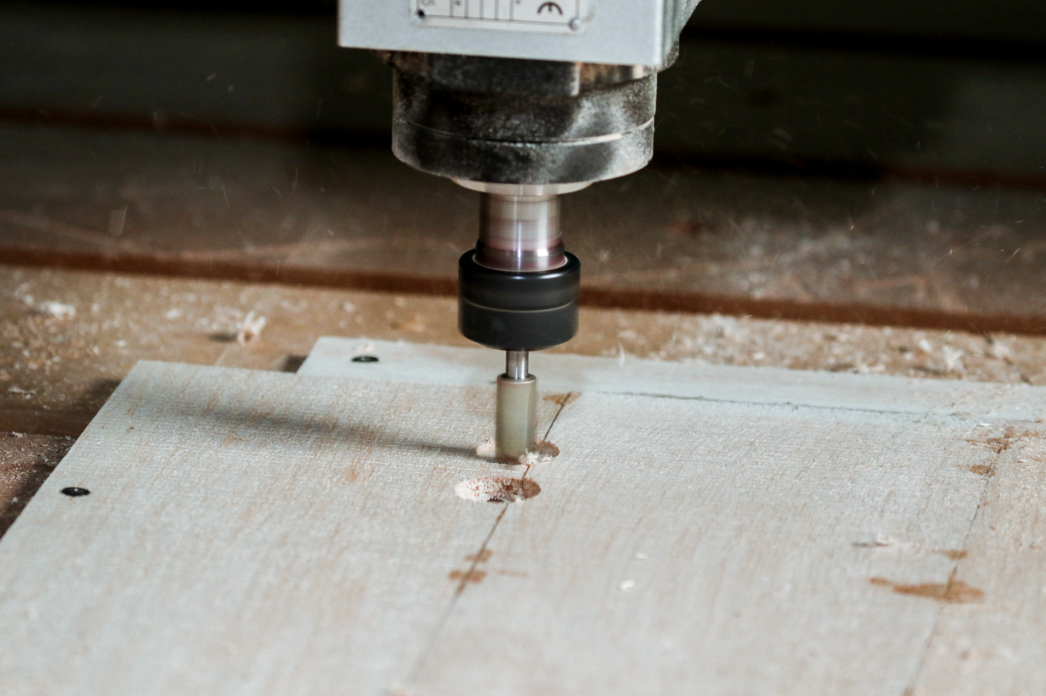
You will learn the basic and useful knowledge of end milling and the difference between drilling, and how to select the right tool.
What Is End Milling and End Mill Cutting?
End Mill vs Drill Bit: What's the Difference?
Understanding the Differences Between Milling and Drilling: Processes and Capabilities
How to Choose the Right End Mill Cutting Tools
The Benefits of End Milling Operation
Different Types and Applications of End Mill
FAQs about End Milling
What Is End Milling and End Mill Cutting?
End milling is a type of CNC milling that uses a cutting tool called an end mill. End mills feature cutting teeth on the sides and end of the mill, which makes them suitable for both end-cutting and peripheral cutting. End mills can be used for a number of unique applications, including tracer milling, milling profiles, face milling, shape milling, and plunging. The cutters on end mills are capable of making precise cuts, which means that they can be used for many different applications where exactitude is required.
There are different types of end mills, which can be used for various applications. Selecting the correct end mill for the desired purpose is a task that should be completed carefully to get the right tool.
End Mill vs Drill Bit: What's the Difference?
An end mill and a drill bit might seem similar at first glance. However, there are multiple differences between them. They are used for different functions and can't be used interchangeably. It's important to understand how to tell them apart and when it's appropriate to use each of them.End Mill
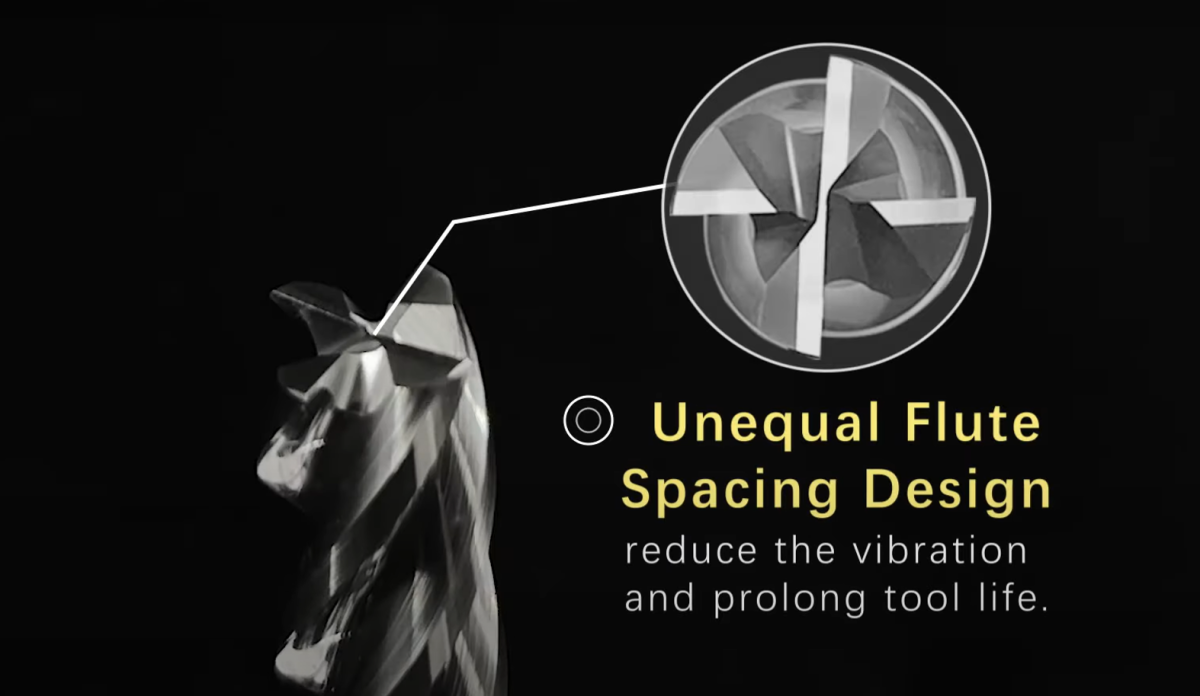
An end mill is designed for sideways cutting. There are various types that can be used for a variety of applications and can create different kinds of cuts. End mills have different numbers of flutes and shanks in varying diameters. There is a choice of shapes, such as ball nose, corner radius, and forming cutters, which can be employed in different ways. For example, flat-end cutters can be used for fine or rough milling and are useful for working on grooves or contours. Ball nose end mills are useful for semi-finishing and finishing and can be used for curved or steep surfaces, among other applications.
Related Article: The Beginners Guide of CNC End Mill (2023 Edition)
Drill Bit
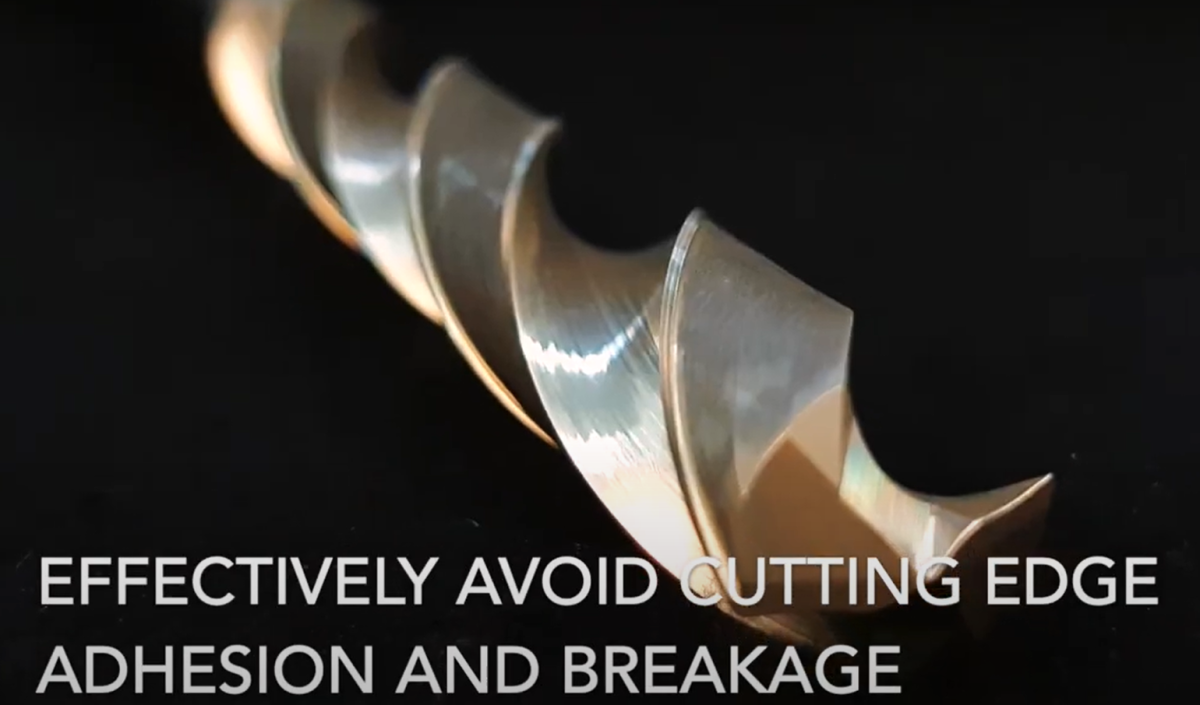
The purpose of a drill bit is to bore straight down into the material that is being worked on. It is used to drill holes of different types, with a variety of drill bit options to meet a range of needs. The choice of drill bit will depend on the material and the project, with multiple choices in different designs and materials. For example, an ejector drill bit or spade drill bit can both be appropriate for metal drilling, while flat bits, auger bits, and dowel bits are all good choices for woodworking.
Related Article: The Guide to Buying Carbide Drill Bits, Choose the right one for your job
Understanding the Differences Between Milling and Drilling: Processes and Capabilities
Definition
Milling and drilling are two different processes, which are both important in manufacturing. In short, drilling is making a hole, while milling allows the creation of walls, slots, webs, and various other features.
Dynamic Movements
Drill bits are rotating and use vertical motions to create holes. Meanwhile, milling also uses vertical movements of the mill cutter but it also employs horizontal motion of the piece being worked on at the same time. When drilling, the piece being drilled is held in place but workpieces can be moved in multiple directions when milling.Precision and Versatility
Milling is able to create more complex shapes, whereas drilling is the best choice when vertical holes are required. End milling can be much more flexible compared to drilling thanks to the multiple cutting edges that end mills have. End mills can have up to 16 cutting edges and are capable of producing high-quality surfaces.Milling Machines
Milling machines are often more accurate compared to drilling machines. They can be used to carry out tasks quickly and accurately through computer control. Additionally, modern milling machines don't produce metal debris or overheat. Milling machines are more versatile than drills and the cost is often about the same.How to Choose the Right End Mill Cutting Tools
There are several things to consider if you want to choose the right tools for any manufacturing project. When you need to select the best end mill cutting tools, you will want to think about the scope of the project, materials, and budget. Firstly, it's important to know whether you need drilling or milling to complete the task that's required.End mill cutting tools may be better when you need to make holes of different sizes. End mills can be the right choice for larger holes too. If you need a flat-bottomed hole, you will need an end mill because normal drills don't have that capability. When you need a flexible and fast tool, end mill cutting can help with rapid prototyping and other requirements.
You will typically want an end mill for slotting, plunging, contouring, tracer milling, profile milling, and traditional roughing. Some things to consider when choosing the right end mill cutting tool include:
- Material – the material that you're cutting will affect which tool you need.
- Operations – is the cutting tool for roughing, finishing, contouring, etc.
- Number of flutes – if cutting non-ferrous materials, two or three flutes is typical, more flutes may be used for certain applications, including roughing, finishing, and slotting.
- Tool dimensions – cutter diameter, length of cut and reach and tool profile are all important factors.
- Coating – coated tools can help to boost performance for some applications
Related Article: How to choose the right Coating for your End Mill?
The Benefits of End Milling Operation
End milling offers a number of excellent benefits. It's worth considering for a number of applications to achieve the desired results. End mill cutting can both remove large amounts of material and be used to refine the surface and help finish the material. Here are some of the top benefits of the end milling-cutting process.Versatility and Flexibility
End milling can be used for a broad range of applications, which makes it a versatile and flexible manufacturing process. Being able to apply it to several different things means that owning end mill cutting tools makes many types of work possible and ensures it's a wise investment.Precise and Accurate
Precision and accuracy are both important in manufacturing, although they matter more for some purposes than others. As it is a CNC milling process, end mill cutting is guided by computer coding and software. The result is that the movements and results are highly precise and accurate, as greater precision can be achieved compared to doing something by hand or with purely human guidance. Accuracy is essential for many purposes, including when there are very specific requirements for certain parts and products.Applicable to a Range of Materials
End milling can be used on a range of materials. It's a popular choice for cutting metals, but it can also be used for nonmetals and other solid materials, including wood or plastic.Fast and Efficient
When you need speed and efficiency, end milling can provide. Once the machine has been given its instructions, it will quickly carry out the cutting to produce the intended results. Because the process is computer-controlled, it increases efficiency by reducing the need for human input and therefore cutting down on human error. The automated process can run for a long time, making it easier to manufacture things quickly.Capable of Complex Tasks
Complexity is no challenge for end mill cutters. End milling works for complex specifications thanks to its capability for tackling a wide range of different jobs.Different Types and Applications of End Mill
Different types of end mills can be used for different purposes. The various types can be differentiated by their shapes, materials, applications, and number of flutes.End Mill Shapes
Each shape can work well for different applications.- V-bits – featured a V-shaped end, suitable for small cuts and details.
- Square end – suitable for general-purpose milling.
- Ball end/flat end – rounded cutting edge for a smoother finish, useful for contours and more.
- Fishtail end – cutting teeth on one end, helping to reduce splitting, and useful for contours, flat bottoms, plunge routing, etc.
End Mills By Number of Flutes
The number of flutes affects the capabilities of the end mill. The most common options are 2, 3, and 4 flutes.- 2 flutes – suitable for wood and aluminum
- 3 flutes – less common, but have good chip removal
- 4 flutes – a good choice for harder materials
End Mill Materials
The choice of material is important because it dictates the durability of the end mill, its cost-effectiveness, and its capabilities.- High-Speed Steel (HSS) – cheaper than solid carbide but less durable and with lower speed capabilities.
- Tungsten Carbide – more expensive but tougher and with higher resistance to heat, as well as wear and tear, they are often used in industrial applications.
- Cobalt – another more expensive option (compared to HSS) but with excellent durability and a long lifespan.
- Solid Carbide End Mills Cutter – high-performance Solid Carbide End Mills are suitable for any mill cutting operation and material.
FAQs about End Milling
Q1: What Is CNC Milling?
A: CNC (Computer Numerical Control) milling is a machining process used for shaping with rotating cutters. The tool is controlled with a computer, which enables high-quality finishes and high levels of detail to be achieved. The CAD (Computer Aided Design) file provides instructions for what the milling machine should cut so that very little human input is required to complete the task. CNC milling machines can be used to mass-produce parts in different materials, achieving both speed and an array of possible shapes and designs.Q2: What are the key benefits of end milling operations in manufacturing?
A: End milling offers versatility, precision, applicability to various materials, speed, efficiency, and the capability to handle complex tasks, making it a valuable process in manufacturing.Q3: What are the key points to choose the best cutting tool?
A: Consider factors such as material, operation type (roughing, finishing, contouring), number of flutes, tool dimensions, and coating when selecting end mill cutting tools for your manufacturing project.■ More Information & Tips about CNC End Mill:
Related Article: Master Guide of CNC Milling: Process & Application
If you are new to CNC milling, you have probably heard of this term but be unsure what it means. In this article, you will find all the information you will need to understand what CNC milling is, how it works, its applications, advantages, and more. Read on to discover everything you need to know about CNC milling.
Related Article: Master Guide of Roughing & Finishing Cut in Machining (Differences & Usage)
If you are new to CNC milling, you have probably heard of this term but be unsure what it means. In this article, you will find all the information you will need to understand what CNC milling is, how it works, its applications, advantages, and more. Read on to discover everything you need to know about CNC milling.
About Speed Tiger |
Speed Tiger is a professional manufacturer of Carbide Cutting Tools and offers OEM Services, having rich experience in producing carbide cutting tools and processing consultants for more than 24 years.
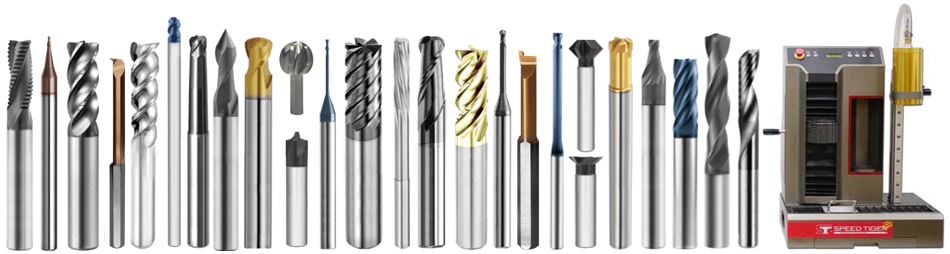
Established in 1998, Speed Tiger specialized in the production of precision carbide end mills, drills, turning tools, thread mills, and other tungsten carbide steel customized cutting tools. Speed Tiger crafts cutting tools at extreme nanometer precision +-2㎛ to the exact, enabling to achieve professional cutting quality.
Visit our shop to find out more, or check out our solution to continue learning.
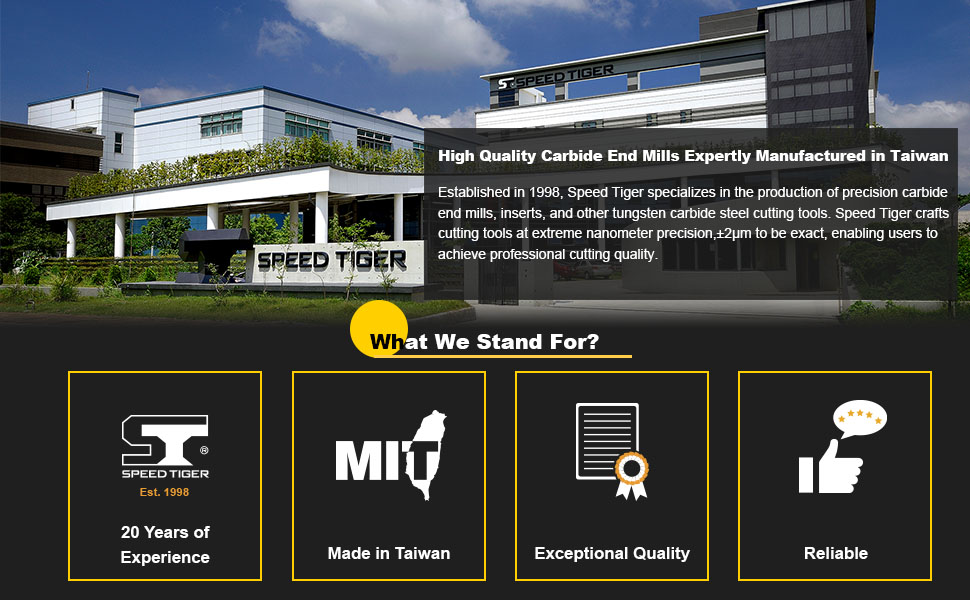
OTHER SOLUTIONS
-
Master Guide of CNC Milling: Process & Application Posted 2023-06-07